On Board the Shinkansen
Shinkansen Nozomi Super - Express
A Culmination of Japanese Quality
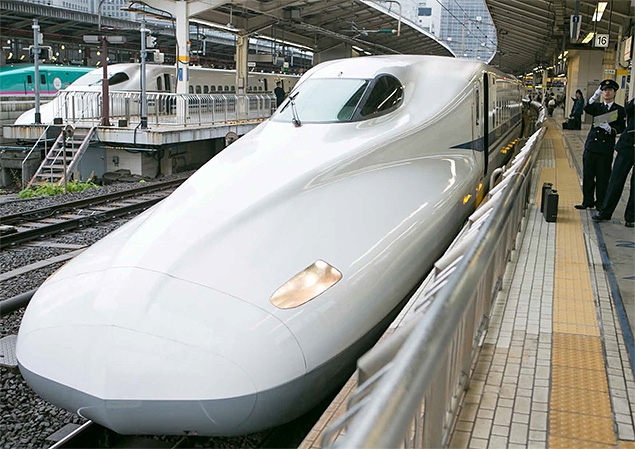
On October 1, 1964, the Tokaido Shinkansen began running between Tokyo and Osaka as Japan’s first high-speed railway.
Today, it continues to operate at speeds of up to 270km an hour, and after nearly half a century has yet to see any major accidents.
The cars barely shake, offering a smooth, comfortable ride, and the first train of the day is spotless, with everything in perfect order.
They invariably run on time.
The Shinkansen is truly the culmination of Japanese quality.

Noriko Abe is responsible for supervising all train car cleaning. Since cleaning can also affect operating schedules, she needs to be on her toes every day.
Cleaning staff in matching pink uniforms line up on the platform to await the next Shinkansen’s arrival.
Standing in front of the doors, they greet each arriving passenger with a smile, and once all passengers have disembarked, move quickly into the cars to begin cleaning. About 12 minutes are allotted from the time of each train’s arrival to complete the job, but considering the time needed for disembarking and boarding of passengers, in reality they have closer to eight or nine minutes.
Cleaning takes place in this brief time in the following order. First, the workers collect empty cans, plastic bottles, food wrappers, and other larger trash left on the seats. They return all of the seat backs to their original position, then flip them so that every seat is facing the direction of travel. They remove the seat back covers, then distribute new ones a few at a time across the seats, putting each one in place before sweeping the seats of any smaller refuse, while also wiping down window ledges and armrests with a cleaning cloth. Window blinds are set in position, floors swept, and a mirror is used to check the overhead luggage racks for items that might have been left behind. Finally, the entire car is inspected.
While this is going on, trash receptacles in each car are emptied.
Toilets and washstands are cleaned, smoking rooms are cleaned and ashtrays emptied, blankets and magazines rearranged in the first class Green Cars, and the train resupplied with water.
One area that requires particularly close attention in the cleaning process is damp seats. Once a spilled drink has soaked into a seating surface, it can be very difficult to detect with the naked eye, and this is why they’ve developed a broom with a built-in dampness sensor. Thanks to this invention, staff no longer overlook even the slightest hint of dampness on a passenger seat.
Asked about the secret to achieving a quick, high-quality cleanup, cleaning crew supervisor Noriko Abe noted that “What’s important is that everyone carry out their assigned tasks in order and without a mistake.” Everyone performs their tasks according to the manual. If they can do that, nothing gets left behind, and even with shift changes, the teams are able to maintain the quality of their work.
As many as 120 trains in peak season
Each team involved in the cleaning consists of 55 staff. This includes two for each car, four to clean the toilets and washstands, four to clean the smoking rooms, plus three more for the Green Cars. Supplying water and handling trash requires another 11 people, and finally each team also has a supervisor. There are six of these 55-person teams, each of which handles between 15 and 18 trains a day. While they average a total of 88 trains a day, during the summer Obon holidays and other peak seasons, they may clean as many as 120 trains in a single day.
Watching the actual work underway, there is not a single wasted movement, and everyone goes about their tasks with a determined expression.
That seriousness is the flip side of just how little time they have to work, or in other words, a reflection of their awareness that their work can have a real impact on train operating schedules. That responsibility weighs even heavier than any simple time restraints.
Ms. Abe, who is responsible for adjusting cleaning times and assigning staff based on orders from JR Tokai, works constantly to ensure the trains can run on time, which makes it even more difficult to juggle things when trains are running late due to snow or other factors.
“While I keep in mind which teams are doing which tasks on which platforms, and their standby locations, I have to make instantaneous decisions about how those staff are assigned to arriving trains in order to make up for any delay in train operations. Tensions are at their peak at these times, but I also find such situations to be the most rewarding.”
The train leaves on time, the ride as comfortable as always. We may take this convenience and comfort for granted, but it is these professionals who make it possible.
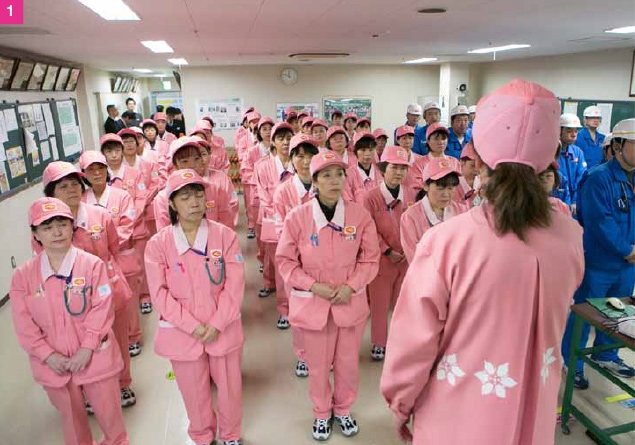
1.Each team starts with a team meeting. Announcements are made, any special precautions are gone over, and the team warms up with calisthenics.