Creating Premium-Quality Coat Fabric that Combines Texture and Color Fastness
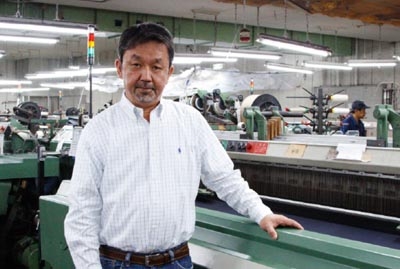
Threne dyeing is known for producing superior texture quality and color fastness. However, this method requires a high level of skill, and in recent years such dyestuffs have become hard to find.So why has this company persisted in using threne-dyed fabric?
(Photo) President Tamio Nohara of Daiwa Intertech, a dyeing and weaving company that was established in the late nineteenth century.
One method for dyeing fabrics is threne dyeing.
“With threne dyestuff, fabrics don’t fade as easily, even with sun exposure, and the colors stay fast in the wash. They’re resistant to getting dirty from exhaust gases and so on, and the colors don’t fade or run easily. They’re well suited for coat fabrics, which need to be tough while also having a high-quality feel.”
According to Hiroshiro Suzuki of Daiwa Intertech, these are the advantages of threne dyeing, but he adds the caveat that it is also a difficult technique.
To begin with, long coats have a very wide surface area, which means that any flaws, such as joins in the thread or dye irregularities, are highly noticeable. The thread used for weaving the fabric should therefore be long and evenly dyed.
A number of steps are essential for threne dyeing long thread. First, the thread, which is the raw material, must be rewound onto a separate bobbin with an appropriate amount of tension. The water used for dissolving the dye in must have a consistent quality, with any metallic ions and alkalis removed. Pump voltage must be controlled to regulate the speed of the water currents in the dye tank. Finally, the dyestuff preparation must be subtly adjusted after measuring the temperature and humidity. If any one of these measures is not performed, dyeing irregularities will appear in the thread.
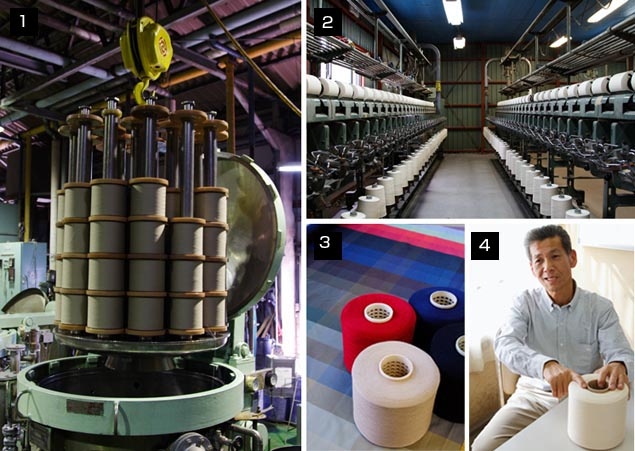
1. Freshly dyed thread dried with hot air. 2. Thread is rewound for easy dyeing. 3. Beautifully threne-dyed thread and fabric samples. 4. Hiroshiro Suzuki has forty years of experience with threne dyeing.
Because of the amount of work involved, over the last thirty years many dyeing factories have shifted to using simpler reactive dyes. However the president of Daiwa Intertech, Tamio Nohara, believes that the beauty of threne dyeing lies in the interweave of the vertical and horizontal colors, and opened out a coat to prove his point.
And opened oconsists of a brown vertical and yellow horizontal thread, i.e., iti.read,vertical and yellow ly colored threads. So the color of the fabric changes in appearance depending on how the light falls on it, or the angle of the cloth, and you get an iridescent effect like this. It vastly improves the sense of quality and the color depth.
When you see people wearing the same color coat or jacket in the same style, the differences in their quality and appearance become obvious. This difference can be explained by the potential of the material.
At Daiwa Intertech the dyed yarn is made up into fabric at the companyn iweaving mill. A high-quality coat requires a high-density fabric of 170 warp threads and 100 weft threads per inch.
170 warp threads and 100 weft threads per inch.ic ding on hent quality, with ion, and there has to be less than five flaws from cut threads.”
It sounds like an extremely difficult task to work for ten hours without cutting any threads while weaving at high speed. In recent times a stream of manufacturers have withdrawn from the accreditation program because they are unable to overcome this difficulty. Dye irregularities and cut threads cannot be tolerated because they spoil the fabric with unwanted flaws and streaks. Daiwa Intertech is able to carry out this process because of its know-how and experience in weaving heavyweight fabric, which it began accumulating before the Second World War.
“Even under difficult conditions, we aspire to make a unique fabric that embodies the requirements and sensibilities of designers and planning coordinators,” says President Nohara. In this way high-quality coat manufacturing is sustained by determination and skills acquired over time.
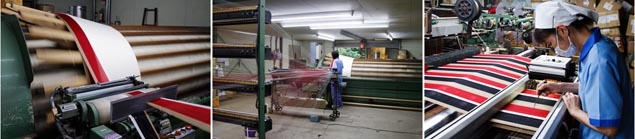
(Left) The warping machine turning at high speed. (Middle) Thread being fed into the warping machine from racks in the foreground. (Right) Every single thread is inspected individually.