TECH & CULTURE
Development of an Ultra-compact Gas Turbine Capable of Generating Large Amounts of Power Anywhere
A promising technology for powering humanoid robots?
March 23, 2015

In addition to the turbine placed in the front center, the photo also shows the fuel feed (upper right), the controller (upper left), and an air inlet and a noise canceller to the right of the turbine and another noise canceller on the left.
The entire system including the case weighs about 13 kilograms but further miniaturization will reduce the size of the case by half and slash the weight to eight kilograms.
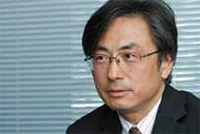
Kosuke Isomura, Engineering Head, Corporate Business Development Division, IHI Corporation
Dr. Isomura’s extensive range of R&D experiences includes the development of micro energy and the development of aircraft engines. His current focus is the commercialization of his ultra-compact gas turbine.
I was ushered into a reception room at IHI’s headquarters in Toyosu, Tokyo. I asked Dr. Kosuke Isomura, Engineering Head of IHI’s Corporate Business Development Division, if I could take a look at this gas turbine. I thought I would be escorted into a lab or workshop to view the machine in operation, but instead Dr. Isomura pointed to a duralumin case in the corner of the room. “Over there,” he said matter-of-factly. The case housed an ultracompact gas turbine power generation system. I was pleasantly surprised to see a gas turbine at work in an ordinary place like a reception room.
The metal mass with a dull shine on it in the front center of the case was the gas turbine. As Dr. Isomura turned on some switches in succession, the machine emitted a shrill sound. This noise was almost completely removed by noise cancellers and the sound of the cooling fans placed on both sides of the case, but the shrill definitely resembled the sound of a jet engine. In the meantime, the revolution speed of the turbine rapidly increased. When it reached 400,000 revolutions per minute, Isomura flipped the switch for some electric bulbs, and voila, the bulbs began emitting glaring light in an instant.
“The output you witnessed just now was 200 watts, but the system is designed to generate up to 400 watts,” Dr. Isomura explained. “It can achieve up to 470,000 revolutions per minute on a stable basis.”
The sliver case became very hot as I listened to his explanation. But the heat wasn’t accompanied by any unpleasant noise. The gas fed into the system came from a cartridge-type compressed gas cylinder of a type often used on hiking trips.
Aiming to become a power source for robots
ASIMO and a score of other robots are currently being developed. One of the challenges faced by robot developers is finding suitable batteries, and this issue will become increasingly pronounced as development reaches more advanced stages.“ASIMO, as it is now, requires about 500 watts of power. Developers are so preoccupied with researching visual cognition and movement that they pay little attention to the battery systems. They just make do by using the batteries currently on the market. You take one of these batteries, charge it for half a day, and your robot will only work for thirty minutes or an hour. Imagine a robot on a disaster rescue mission running on this battery. If it lasts for only an hour, it may attract some curious attention, but it definitely won’t do much good. A humanoid robot that can assist people needs a battery capable of providing power all day.” According to Dr. Isomura, an energy density of around 500Wh/kg or a power density of around 200W/kg would be the minimum requirement for a robot capable of performing human tasks for a few hours on a continuous basis. This energy requirement is best met by an ultra-compact gas turbine, as it does not suffer the disadvantages of rechargeable batteries (lithium-ion batteries) such as low running time despite high power density, or fuel cells, whose substantial weight makes them unsuited for mounting on robots.
Characteristics of Power Sources by Type
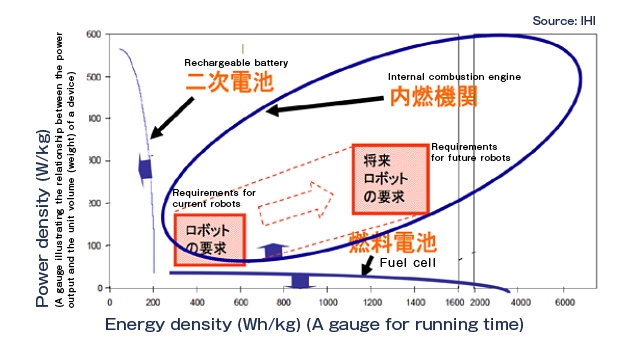
Advantages of gas turbines
One of the most common internal combustion engine mechanisms is the reciprocating engine found in motor vehicles. It converts fuel into pressure, which in turn forces pistons in cylinders to move and rotate the crankshaft. Energy is extracted in the form of crankshaft power. In contrast, the gas turbine mechanism converts thermal energy into kinetic energy by directing the gas flow through a nozzle, and the high-speed thrust generated in the process rotates the turbine with its impact and reactive forces. The main difference between the two is that the former mechanism is based on intermittent combustion while the latter relies on continuous combustion.“Reciprocating engines invariably result in uncombusted gas, as the temperatures attained by the mechanism vary widely. In contrast, the temperatures obtained by gas turbines are more stable, and this stability allows us to concentrate primarily on the points in the structure where we would ordinarily focus and design the system in accordance with heat loss trends and the distribution of temperature.”
Moreover, friction losses are an unavoidable and unchangeable characteristic of reciprocating engines. In gas turbines, the rotor itself is not in contact with anything except the bearing, and the friction caused by this contact can be eliminated altogether with the use of an air bearing, which allows the rotor shaft journal to be suspended in the air.
The quest for an ultra-compact gas turbine began in 2000 as a study project in collaboration with Tohoku University. The key challenge the team faced from the start was the number of revolutions produced at the bearing. The performance of the system depended upon the speed achieved at the outermost part of the moving component.