TECH & CULTURE
Ultrasonic cutting technology opens up infinite possibilities
Willing to try and cut anything
March 25, 2017
Approximately 10 billion sheets of nori are consumed in Japan every year. Nori is laver, an edible seaweed that is compressed into paper-like sheets which are used for making all types of sushi rolls, wrapping rice balls and rice cakes, or shredded as a garnish for soup and other Japanese dishes. It is an integral part of Japanese cuisine.
Over the last ten years, rice balls purchased at convenience stores have increasingly become a regular part of the modern Japanese consumer's diet.
Rice balls are a convenient meal, the Japanese equivalent of sandwiches. A handful of rice is shaped into a ball with a mouthful of filling in the center, and wrapped in nori to hold it all together. In the past, the nori used for convenience store rice balls was poor quality and noticeably tough. But from around 2000 onwards there was a dramatic improvement in the quality of these store-bought rice balls thanks to revolutionary changes in the nori used to make them. The nori became easier to bite off, had a better feel in the mouth and tasted better, too. Behind these improvements lies a surprising technology.
Convenience store nori is perforated by countless holes so small you wouldn’t notice just by looking. It is these holes— which must be of the right size, shape and spacing—that changed the flavor of convenience store nori and added the extra value.
In reality it is not an easy task to create uniformly-sized holes in a split second during the manufacturing process. If the nori is wet or damp it tends to stick like glue, and when powdered nori scatters and clings to the tool making the holes, it dulls the cutting edge. Nori is also a delicate natural ingredient, which will break off into irregular sized pieces if too much force is applied. These were the difficulties that the Kumakura Corporation’s technology helped to overcome.
Kumakura, located in Ota Ward, Tokyo, is a small-scale factory proud of its precision parts machining technology. Its main line of business is commissions for advanced micromachining. Why would such a factory choose to develop the technology for processing something so seemingly unrelated as convenience store nori? Well, it would have to be because the company was already thoroughly familiar with nori and its particular quirks.
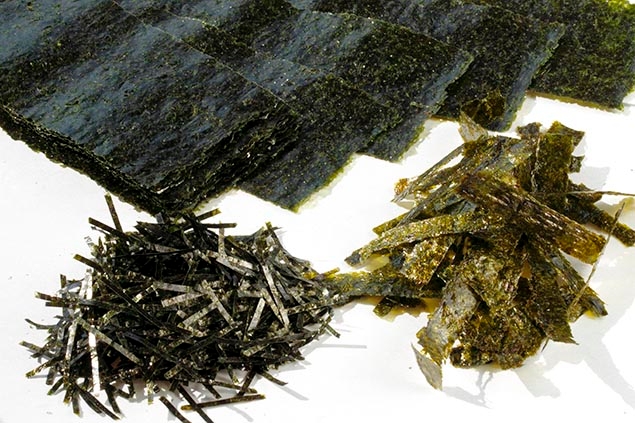
Almost all major nori producers in Japan use Kumakura machines to cut nori. There are machines to cut nori for sushi rolls, flavored nori, gunkanmaki (“warship rolls”), crumbled nori and shredded nori, amongst others. There are also machines that not only cut nori into strips, but also have pattern cutters to make hearts, maple leaves or various other shapes as well. The machines may be slightly more expensive than those of other companies, but many customers come back.
Rice balls are a convenient meal, the Japanese equivalent of sandwiches. A handful of rice is shaped into a ball with a mouthful of filling in the center, and wrapped in nori to hold it all together. In the past, the nori used for convenience store rice balls was poor quality and noticeably tough. But from around 2000 onwards there was a dramatic improvement in the quality of these store-bought rice balls thanks to revolutionary changes in the nori used to make them. The nori became easier to bite off, had a better feel in the mouth and tasted better, too. Behind these improvements lies a surprising technology.
Convenience store nori is perforated by countless holes so small you wouldn’t notice just by looking. It is these holes— which must be of the right size, shape and spacing—that changed the flavor of convenience store nori and added the extra value.
In reality it is not an easy task to create uniformly-sized holes in a split second during the manufacturing process. If the nori is wet or damp it tends to stick like glue, and when powdered nori scatters and clings to the tool making the holes, it dulls the cutting edge. Nori is also a delicate natural ingredient, which will break off into irregular sized pieces if too much force is applied. These were the difficulties that the Kumakura Corporation’s technology helped to overcome.
Kumakura, located in Ota Ward, Tokyo, is a small-scale factory proud of its precision parts machining technology. Its main line of business is commissions for advanced micromachining. Why would such a factory choose to develop the technology for processing something so seemingly unrelated as convenience store nori? Well, it would have to be because the company was already thoroughly familiar with nori and its particular quirks.
The acquaintance with nori began from a whisper
The story goes back fifteen years. Over drinks one day at a gathering of business people from different industries, someone was heard to sigh over the lack of machines that could easily cut nori.One of the people present overheard this, and could not let it go.
That was the current chairman of Kumakura, Ken’ichi Kumakura.
Next morning, he rang the person in the nori industry who had made the comment and was called in that very same day. The sight that met him at the nori processing plant was one from a bygone world he could never have imagined: the veteran part-time female employees were all cutting the nori by hand. This was also a cause of vexation for their families, as the nori that was scattered in the process stuck to the workers’ skin and made it smell. That was how it began, and eventually Chairman Kumakura designed a machine to cut nori. One that could be used by anyone to cut nori in exactly the same way.
At that time things were changing. Highgrade nori was no longer selling as an item for the traditional exchange of gifts at New Year and midsummer, and instead there was a shift to demand for industrial-use nori because of convenience stores and conveyor-belt sushi restaurant chains. In line with this demand machines that could cut nori quickly became indispensable. The machine that was developed by Kumakura at this time was eventually adopted by other major nori producers, and now occupies a good 40 percentage of the domestic market share. It is thanks to this machine that consumers can easily buy nori of varying sizes off the shelf.
As for the convenience store nori, the company’s success in developing technology to make holes in nori can be attributed not only to having previous experience in developing nori cutting machinery, but also the fact that it excelled at micromachining technology.
As mentioned earlier, nori becomes soft over time. Even when making holes with a drill-like cone-shaped blade, eventually moisture causes it to clog up. After three years of repeated discussion with nori producers, the company succeeded in making holes in nori through the use of a square blade tip.
That was the current chairman of Kumakura, Ken’ichi Kumakura.
Next morning, he rang the person in the nori industry who had made the comment and was called in that very same day. The sight that met him at the nori processing plant was one from a bygone world he could never have imagined: the veteran part-time female employees were all cutting the nori by hand. This was also a cause of vexation for their families, as the nori that was scattered in the process stuck to the workers’ skin and made it smell. That was how it began, and eventually Chairman Kumakura designed a machine to cut nori. One that could be used by anyone to cut nori in exactly the same way.
At that time things were changing. Highgrade nori was no longer selling as an item for the traditional exchange of gifts at New Year and midsummer, and instead there was a shift to demand for industrial-use nori because of convenience stores and conveyor-belt sushi restaurant chains. In line with this demand machines that could cut nori quickly became indispensable. The machine that was developed by Kumakura at this time was eventually adopted by other major nori producers, and now occupies a good 40 percentage of the domestic market share. It is thanks to this machine that consumers can easily buy nori of varying sizes off the shelf.
As for the convenience store nori, the company’s success in developing technology to make holes in nori can be attributed not only to having previous experience in developing nori cutting machinery, but also the fact that it excelled at micromachining technology.
As mentioned earlier, nori becomes soft over time. Even when making holes with a drill-like cone-shaped blade, eventually moisture causes it to clog up. After three years of repeated discussion with nori producers, the company succeeded in making holes in nori through the use of a square blade tip.
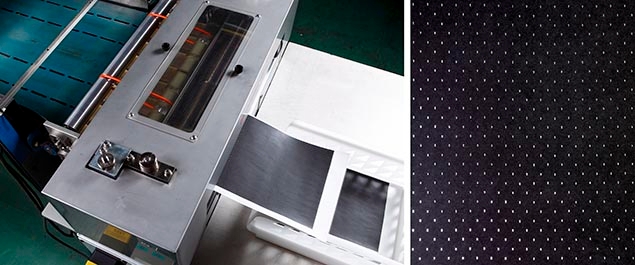
The ∞ Infinity sheet nori perforator. All Kumakura machines are given unique product names by Chairman Kumakura. This machine puts microscopic slit holes in the nori fibers that change the texture of the nori dramatically.