Hinoki-Buro : Ancestral workmanship brought to perfection along the years
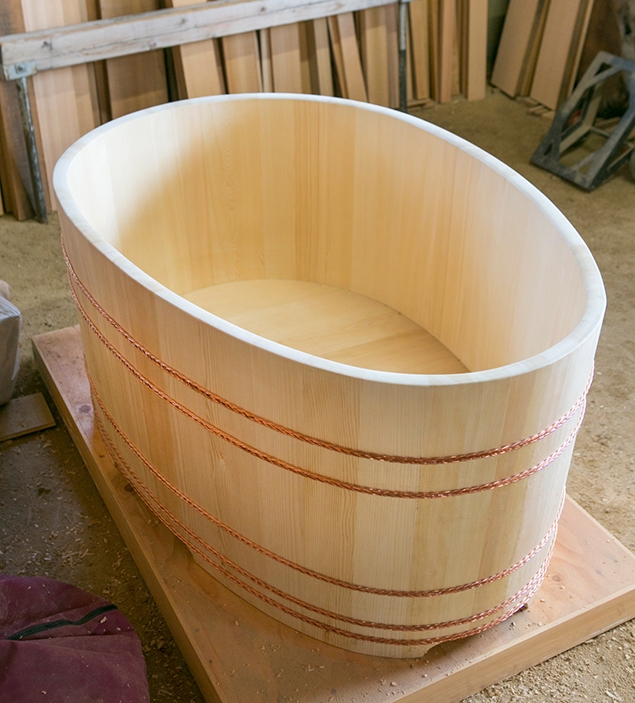
The egg-shape model is the latest creation of Koichi Yoshida. When you lay your back on the narrow side and stretch your legs, you have the impression of dipping in a large tub while having great dorsal support. On the wider side, you have more back room, but can enjoy a very comfy cocoon sensation.
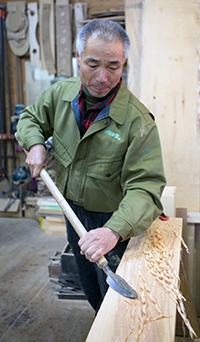
Koichi Yoshida is the
President of YOSHIDA
SHOTEN, which he founded
in 1986, transforming his
father’s wood shop into an
ancient Beni-Hinoki bathtub-
making company.
So why do we call wooden bathtubs “Hinoki-Buro”? Koichi Yoshida explains, “The cream of wooden bathtubs is one that is made of Taiwanese ancient red cypress, “Beni-Hinoki.” This wood comes from giant trees that grow up to 25m high with 3 to 4m of diameter, in the highlands of Taiwan, for 1000, sometimes 3000 years.” The lumber of these “Ents” as Tolkien would put it, has been forbidden 30 years ago. However, Yoshida’s father, who owned a wood shop in Kyoto since 1934, had accumulated a reasonable stock before that date. So in 1986, Yoshida transformed his family business into an ancient Beni-Hinoki retailor and started the sales of wooden bathtubs. This material being very expensive from the start and becoming rarer nowadays, there is no surprise when Yoshida confirms that not so many people can afford them. “We can only find Taiwanese ancient Beni-Hinoki here in Japan, now. And we are only a few rare makers.” This wood’s properties are the absolute attributes to bathtub making. First, its shape never changes. Then it contains essential oils that are bactericide and protect from about any known microbe, germs, mould, or viruses. Last comes its aroma…
The Yoshida quality is a pride
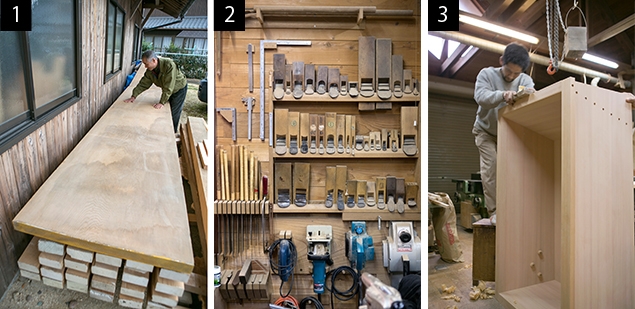
1. When the design and material are defined, the wood is meticulously chosen by Yoshida. An ancient Beni-Hinoki plank makes generally 60cm by 4m.
2. The main plank is cut into small pieces that are chiselled, sanded, then assembled together with special glue, to shape a curve or an angle according to the design.
3. Once assembled, the tub is worked with planing, bevelling, and finally extremely precise sanding, which brings all the visual and tactile quality to the tub.
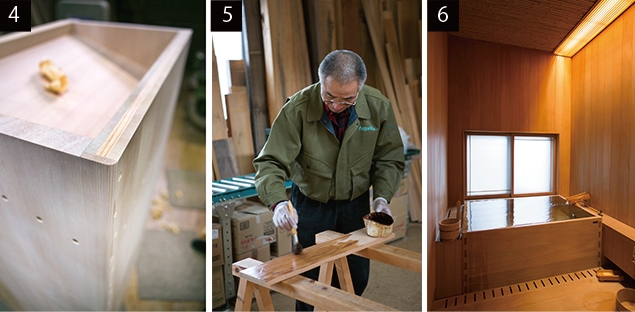
4. The side panels vary in width from 33 to 40mm. Larger edges may give a luxury look, but they don’t affect quality. What differentiates quality: the bottom layered with three planks.
5. Some customers require a lacquered layer. The tub is then dismantled and natural lacquer is added to each part, one layer a day, during 8 days. The type of lacquer that is used keeps the wood breathing and doesn’t affect its bactericidal properties.
6. It is important to keep a few centimeters of space on each side and under the tub, to make it dry faster. Wood lasts well when completely immerged or in all-dry environments. Its only rots when staying for loo long “in-between.” Let’s not forget to wipe the water off after use.